Vortex ups va rs
Top sales list vortex ups va rs

Latest Offers

Kandhura (Federally Administered Tribal Areas)
Eagle Racking India is a leading provider of high-quality mezzanine floor in Lucknow, offering cost-effective and space-efficient solutions for warehouses, factories, and commercial establishments. Our mezzanine floors are designed to maximize vertical space utilization, providing an additional floor without the need for expensive building expansions. Constructed with heavy-duty steel and premium-quality materials, our mezzanine floors ensure durability, strength, and safety. They can be customized to meet specific load-bearing capacities and operational requirements, making them ideal for storage, office setups, and retail spaces. Read more: https://eagleracking.com/lucknow/mezzanine-floor
Rs 0,0
See product
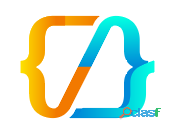
Rawalpindi (Punjab)
Programmers Lab Training Institute is the best IT training institute for computer short courses in Rawalpindi Islamabad . Our mission is to empower every student with IT skills and knowledge. With a wide array of job oriented computer short courses, we ensure that our students are prepared to succeed in their careers. Our computer short courses include Website Designing Course In Rawalpindi, React-Native course,SEO course, Graphics Designing course, FUll Stack Web Development Course In Rawalpindi Social Media Marketing course, Digital Marketing course, Php course, Sql, Video Editing course, Content Writing course, Basic IT, course ,MS Office Course, and many more short courses.
Rs 0,0
See product
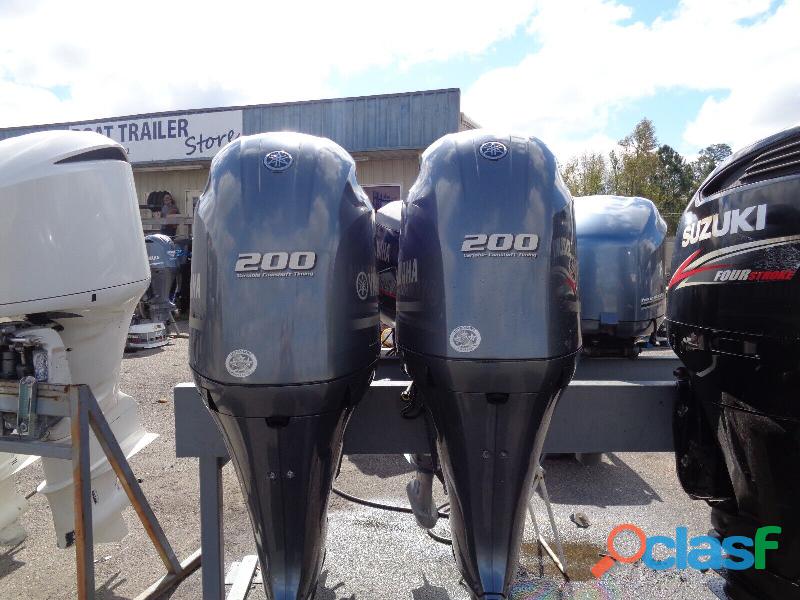
Pakistan (All cities)
We have the Outboard Boat Engine OXE. Yamaha We are specialized in the sales of full metal scrap/ recycling material such as ac/fridge compressor , Ceramic Cpu Gold Processor Scraps , H.M.S 1&2, Copper wire scrap,Drained Battery Lead scrap in the UK (LONDON).We have all our product fully ready for sales in good quantity and quality also to be shipped out for our buyers.For Booking : https://wa.link/og0sgp Whatsapp: +15806151130
Rs 150.000,0
See product
2 photos
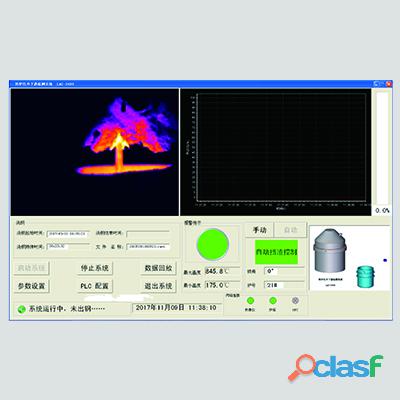
Pakistan (All cities)
Overview The infrared converter slag detection system uses a far-infrared thermal imager to monitor the situation of converter tapping in real time, and is connected to the main control computer in the electrical room through the conversion and transmission of video signals. The radiation intensity in the infrared wavelength range of 7-14um is different to distinguish molten steel and slag. In the later stage of the converter tapping, the molten steel gradually decreases, and the steelmaking slag is involved in the molten steel and flows out of the tapping hole. After the thermal imager recognizes the steelmaking slag in the imaging temperature measurement, it will give an alarm according to the slag content ratio threshold set by the software. The thermal imager will start the slide plate to close the tapping hole, so as to realize the control of the slag in the converter tapping, and ensure the maximum yield of molten steel and the minimum control of the steelmaking slag content. The effect of slag detection in converter tapping is of great significance to the control effect of the slag amount. The converter slag detection and control system developed by our company conducts non-contact monitoring of the tapping steel flow through the far-infrared detector thermal imager. It can detect the slag condition in real time and output an alarm signal and control system, which can replace manual visual inspection and provide accurate, efficient and stable slag detection effect. When the system finds the slag, the intelligent control unit quickly makes a judgment of lifting the furnace and blocking the slag and outputs an alarm signal. As shown in Figure 1, the system includes thermal imager, front purge protection box, front electrical box, power distribution cabinet, main control monitor, monitor of rocking furnace chamber, sound and light alarm, infrared converter slag monitoring software system, etc. The features of thermal imager 1. The temperature measurement range is 200°C ~ 2000°C, high temperature measurement accuracy, and multiple temperature measurement intervals can be set. 2. High-resolution thermal imaging system, the imaging picture is clear, and the imaging color can be freely marked according to the set temperature. 3. With hot zone alarm function, the alarm zone and temperature range can be set arbitrarily. 4. With hot zone tracking function 5. Equipped with special 7~14um infrared filter lens The technical parameters 1. Temperature measurement range: 200°C ~ 2000°C 2. Temperature measurement accuracy: 2% 3. Detection accuracy and alarm accuracy: ≥98% 4. Resolution: ≥ 0.5℃ 5. Pixels: 640x240PT 6. Band: 7~14um 7. Field of view: 7.5°×5.5° 8. Frame rate: ≥ 25 frames/sec 9. Equipment service life: ≥5 years 10. The normal operation rate of the automatic control system: ≥99%
Rs 0,0
See product
3 photos
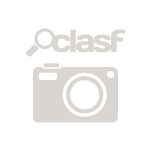
Pakistan (All cities)
China Metal Parts Forging OEM Manufacturer Co., Ltd. (https://www.creatorcomponents.com/) was founded in 2000 by a team of experienced professionals in the forging industry. As a Chinese manufacturer, we specialize in providing high-quality carbon steel and alloy steel metal parts and components for a wide variety of industries. We focus on innovation and engineering excellence to ensure that we meet the highest standards of quality and performance. By utilizing advanced technology and state-of-the-art equipment, we produce products that are durable and reliable, meeting the requirements of both domestic and international customers. Quality is a top priority at every stage of our production process. From inspecting raw materials to conducting 100% final product testing, we ensure all products comply with international standards through our thorough quality control system. As a Chinese manufacturer, we offer customized metal parts to cater to the specific needs of industries such as automotive, construction, and energy. We collaborate closely with clients to deliver tailored solutions that align with their business objectives. At China Metal Parts Forging OEM Manufacturer Co., Ltd., we are dedicated to providing innovative, sustainable solutions and excellent customer service, earning the trust of businesses worldwide as a reliable partner.
Free
See product
4 photos

Pakistan
Our amazing litter was born on 18th of December mum is stunning tri colour and dad is a lemon and white tri both pedigrees dad has five generations blood line with his papers to prove. We have a litter of 9 chunky playful pups all wormed and....
Rs 200,0
See product
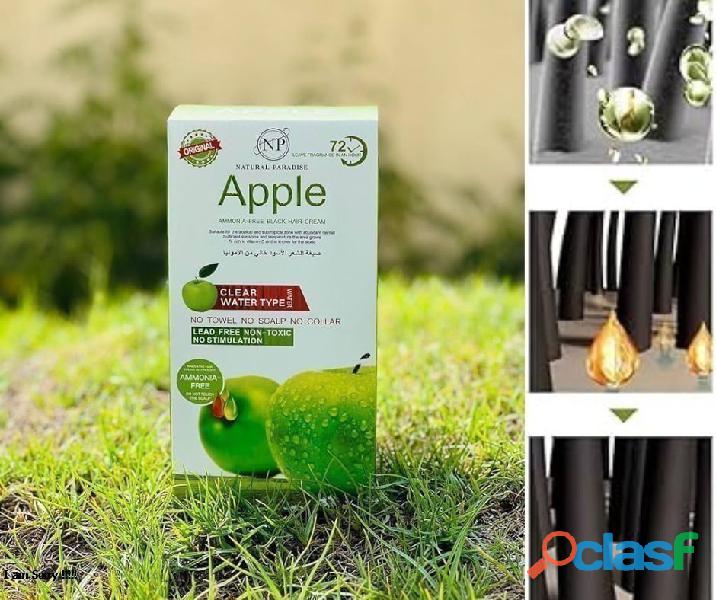
Lahore (Punjab)
Apple Hair Color Price In Pakistan - Quickon.pk Apple Hair Color Price In Pakistan is a hair dye product designed to provide vibrant, long-lasting color while maintaining the health and integrity of your hair. This product is formulated to offer rich, natural-looking color with the added benefits of conditioning and nourishing ingredients. What is Apple Hair Color Price In Pakistan? Apple Hair Color Price In Pakistan is a professional-quality hair dye that offers a wide range of shades to suit different hair types and preferences. The formula is enriched with conditioning agents and natural extracts that help protect and nourish the hair during the coloring process. It is designed to deliver vibrant, long-lasting color with a natural finish. https://quickon.pk/product/apple-hair-color-price-in-pakistanhttps://quickon.pk/product/feg-plus-hair-growth-sprayhttps://quickon.pk/product/sardar-jee-hair-color-gel-price-in-pakistan
Rs 3.500,0
See product
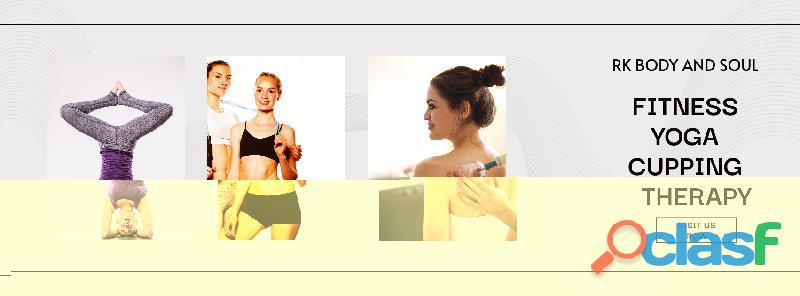
Pakistan (All cities)
We provide best female fitness trainers and best female yoga trainers for women, who wants to stay fit and health from home without going to gym, best ladies gym nearby for housewifes and working women.
Free
See product
3 photos
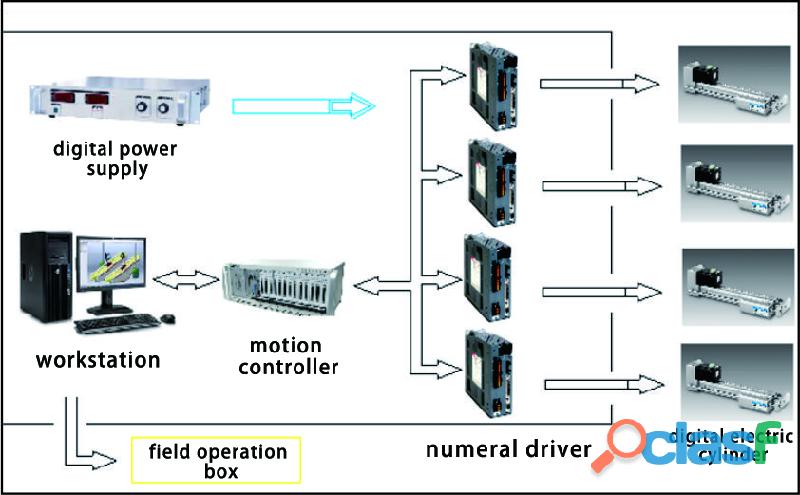
Pakistan (All cities)
Overview In order to meet the needs of producing various specifications of continuously cast products, shorten the time for replacing the mold, and improve the production capacity and production efficiency of the continuous casting machine, the mold online width adjustment system is the key technology for efficient continuous casting. The online mold width adjustment system enables the two narrow sides of the continuous casting slab mold to move inward or outward in small steps until the predetermined width is reached. During the production process, the adjustment of the mold’s width can be completed without stopping the machine. Generally, the online width adjustment of the mold needs to be connected with the online taper measurement of the mold. Only with adjustment and detection can the online adjustment range of the mold be accurately controlled. Fig 1 Mold online width adjustment system The components of the system Workstation: host system, system width adjustment control, taper detection. On-site operation box: real-time display of the current control status, manual operation to adjust parameters. Digital Electric Cylinder: Precise digital control of electro-hydraulic drive cylinder, which can achieve high-precision quantitative control. On-line measurement of taper: Install it on the narrow-face copper plate of the mold, and monitor the taper of the narrow-face copper plate in real time. Cooperate with the detection feedback control of the width adjustment system, so as to achieve high-precision adjustment. FIG 2 System block diagram The technical parameters Adjustable range: 0-1250mm (unilateral) Control accuracy: 0.02mm/0.05mm/0.1mm Step resolution: 0.01mm/0.02mm Running speed: 0-10mm/s Power: 3.5KWl 16-bit encoder: 65536 pulses Weight: 25Kg Shell: high-strength aluminum alloy FIG 3 Syetem software interface The functions of the system Realize online width adjustment function Realize the online real-time monitoring function of mold taper Continuous casting production adjustment and non-stop production One-key operation in the main control room, automatic completion High adjustment accuracy and fast speed The interlock control of the continuous casting steelmaking system can realize automatic steel pouring
Rs 0,0
See product
3 photos

Pakistan
imported Friesian 4 yr old mare for sale. This filly has been backed a few months ago in Holland just for 2 weeks and then came to the uk. advertised due to her needing more one to one. the most amazing mover and really one to be graded and could do well. sad sale as just overstocked. no bargain hunters need to inquire pls as I won't accept offers price is firm. No novices pls. this mare is not for the pussy due to being a little worried with mounting but will settle quick. extremely low inbreeding only 0.39% her sire is the top stallion Sjouke 453 dam is Katrina who is out of Sierk 326
Rs 50.000,0
See product

Gujrat (Punjab)
Looking for the Best PPC Company in Delhi? India Internets is your trusted partner for result-driven PPC campaigns. Our expert team creates highly targeted ads to boost visibility, generate quality leads, and maximize ROI. With data-driven strategies and continuous optimization, we ensure the best outcomes for your business. Choose India Internets for top-notch PPC services today! To Know More: https://www.indiainternets.com/digital-marketing/pay-per-click-marketing-company.html Address:Alliance Web Solution Pvt Ltd. B-112, Sector-64 Noida - 201301 Contact us:+91 9560433318
Free
See product
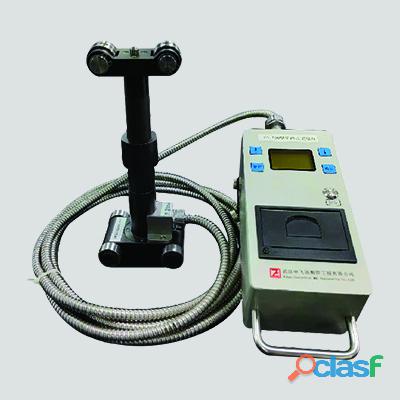
Pakistan (All cities)
Overview The handheld roll gap checker is specially used to measure the length between spherical surface, arc surface and plane (or spherical surface). It is specially suitable for the opening adjustment of the roll gap of the metallurgical continuous casters in various specifications, because the roll gap checker has the advantages of high resolution, accurate measurement, stable data and easy to use. Because the opening accuracy of the roll gap checker will directly affect the quality of the casting block, this roll gap checker is an indispensable testing equipment in the continuous casting equipment, which can fully meet the needs of on-site installation testing and use process verification. When the hand-held roll gap meter smoothly passes through the gap between the guide rolls of the continuous casting machine, the upper measuring contact of the hand-held roll gap checker contacts the inner arc roll and the lower measuring contact touches the outer arc roll. The handheld roll gap checker is used in perpendicular to the roll diameter direction, during the pushing process, when the hand-held roll gap meter is in the tangent plane of the upper and lower rolls, the measured value is the smallest at this time, and this value is the roll gap measurement value. The design of the hand-held roll gap gauge ensures that the upper and lower contacts of the roll gap checker can smoothly pass the measured roll along a straight line during measurement. During the measurement process, the roll gap measuring instrument automatically compares the measured values, and displays the minimum measured value on the instrument display interface, which is the current measured roll gap value. The introduction of different types The measuring range of the split hand-held roll gap checker is 180mm - 400mm This hand-held roll gap checker adopts the design that the measuring body and the display instrument are separated. The measuring body can be clamped by an extension rod, which is suitable for online maintenance and measurement of wider slabs, and it is convenient to use the extension rod to send the measuring body into the continuous casting section to measure inside and we can see measurement data on the checker outside. The measuring range of instrument type handheld roll gap checker is 120mm - 400mm This hand-held roll gap meter is light and compact, and it is convenient to carry during maintenance. The measurement value can be seen immediately after measurement, easy to use, and can be equipped with a short measuring rod. It is suitable for the maintenance and measurement of slab online and offline continuous casting sections. It has data printing function, the measurement results can be printed in real time. The measuring range of thin slab hand-held roll gap checker is 60mm - 150mm This handheld roll gap meter is suitable for measuring the roll gap of CSP continuous casting machine and ultra-thin slab continuous casting machine. It is accurate and easy to use. The technical parameters 1. Measuring range of instrument type handheld roll gap checker: 180mm - 400mm (the range can be customized) 2. Measuring range of digital hand-held roll gap checker: 120mm - 400mm (the range can be customized) 3. Measuring range of hand-held thin slab roll checker : 60mm - 150mm (the range can be customized) 4. Measurement accuracy: 0.01mm 5. Working temperature: -25℃~+85℃ 6. Battery capacity: 5000mAh 7. Charger specification: 12V
Rs 0,0
See product
2 photos
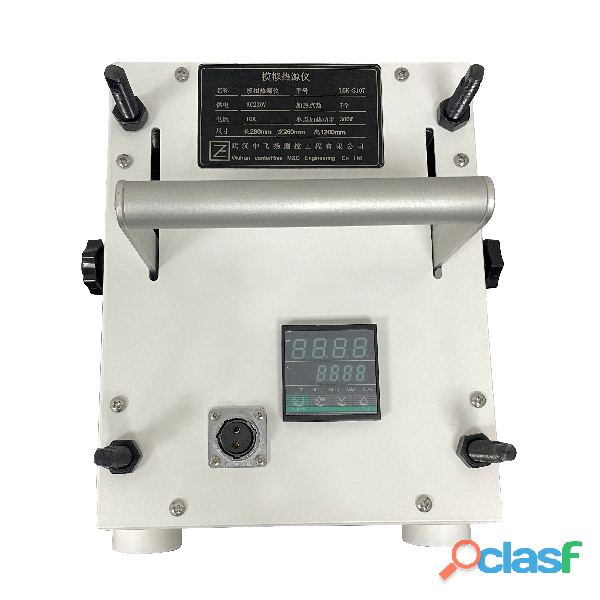
Pakistan (All cities)
Overview: LGK-S107 analog heat source instrument (heating tool) is independently developed and designed by Wuhan CenterRise M&C CO., Ltd. This instrument is a heating and testing equipment used to test the performance of the thermocouples installed in the mold in continuous casting machine. After the installation of the mold breakout prediction thermocouples completed, the analog heat source instrument is used to test these thermocouples before they go online. After the thermocouple is connected to the mold thermocouple detector, the current temperature of each thermocouple point will be displayed. By using our heating device to heat the copper plate point of each thermocouple at a fixed point, the thermocouple will have a synchronous temperature rise and then we can observe the temperature rise curve of the same column of temperature points to see whether the temperature measurement consistency of the column of thermocouples is consistent, so as to judge the overall status of thermocouples installed in the mold. If an abnormal point occurs, it needs to be repaired and replaced, so as to ensure the stable operation of the mold breakout prediction system. The working principle: The heating tool generates high heat by 220v alternating current and the electric heating element. The heat is transmitted to the copper plate of the mold through the copper head to simulate the heat source of molten steel, so that the thermocouples of the mold can sense the temperature change to achieve the purpose of calibrating the temperature measurement system. The composition: Walking trolley mechanism Preloader Pure copper heating contacts PID thermostat High power heating tube high power driver The parameters: Power supply: AC220V 50Hz Total power: 2200W Single point power: 300W Temperature control accuracy: 1°C Temperature control range: 0°C-500°C Common temperature range: 25°C-300°C Heating points: 3 (points can be customized) Heating method: heating tube heating Heating contact material: copper
Rs 0,0
See product
3 photos

Pakistan (All cities)
GoLogica offers complete online training in data modeling that gives professionals the understanding and skills they need to understand data modeling methods. IT specialists, database developers, business analysts, and data analysts who want to become better in creating and managing data structures may benefit from this course. Basic topics covered in the course include entity-relational diagrams (ERDs), data mapping, normalization strategies, and abstract, logical, and physical data modeling. It also covers database design concepts, demonstrating how to build durable, scalable, and effective data models that correspond with business goals. This course, led by industry experts, gives participants practical knowledge through practical assignments, allowing them to apply what they've learned in actual situations. Whether you're new to data modeling or want to improve your existing skills, GoLogica Data Modeling Online Training provides a solid basis for creating and managing successful data models. Enroll in GoLogica Data Modeling Online Training today to obtain the knowledge you need to boost your career in data management and become a certified Data Modeling expert!
Rs 0,0
See product
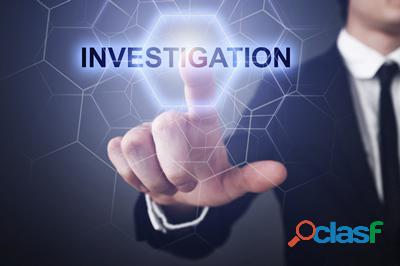
Gujrat (Punjab)
With discreet and reliable surveillance, IonDetective will find out what you want to know. We are professional detectives specializing in obtaining evidence through close observation and time-tested procedures. From cheating spouses to any question or concern that can benefit from being clarified, our company can help bring clear-cut results with total discretion. Our business values honesty, respect, and professionalism; this is exactly why we deserve the truth that you're looking for. Trust us to handle your case with care and precision while keeping the process simple and stress-free. When the truth matters, IonDetective is here to help.
Free
See product