Rubik magic cube
Top sales list rubik magic cube

Latest Offers
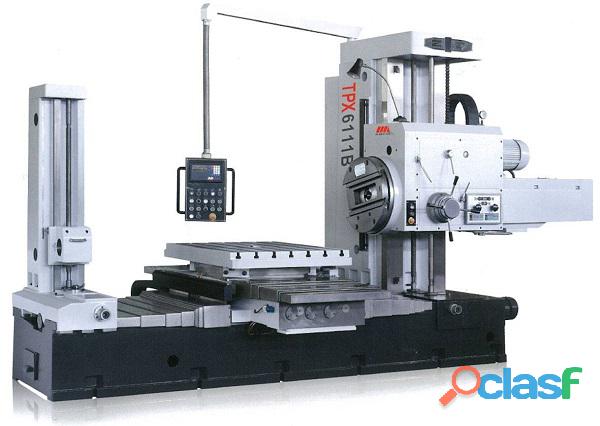
Pakistan (All cities)
Explore the leading manufacturers of horizontal and vertical boring machines, renowned for their precision engineering, innovative technology, and reliable performance. This guide covers top companies offering high-quality machines for various industries, including construction, mining, and manufacturing. Discover key features, advantages, and the latest trends in boring machine design. Whether you're seeking new or used equipment, find trusted suppliers to meet your project needs with ease. https://www.tradebrio.com/exporters/boring-machine.html
Free
See product

Pakistan (All cities)
Rs 0,0
See product
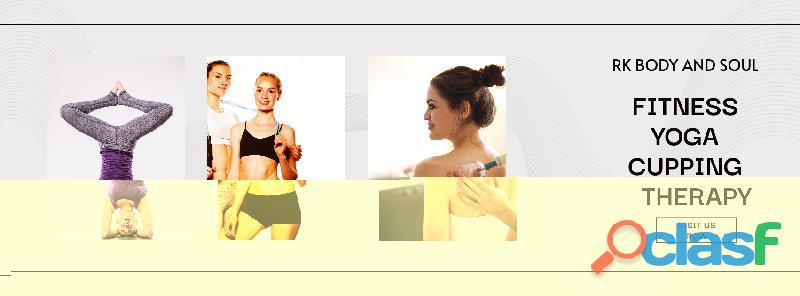
Pakistan (All cities)
We provide best female fitness trainers and best female yoga trainers for women, who wants to stay fit and health from home without going to gym, best ladies gym nearby for housewifes and working women.
Free
See product
3 photos

Pakistan (All cities)
Buy the best herbal supplements & medications in USA online at affordable price. Get free delivery across all states. Order Now!
Rs 30.650,0
See product

Pakistan (All cities)
Rs 0,0
See product
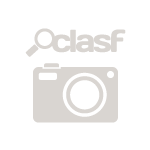
Pakistan (All cities)
Effective Bird Deterrence: Strategically designed bird spikes to effectively deter pigeons, sparrows, and other nuisance birds.....
Free
See product

Pakistan
After a small size Male tri colour beagle smaller than standard size,ideally pocket size or small legged. Must be K.C Registered and come with papers.Ideally Adult or 8months and over.Cash waiting can travel.,
Rs 200,0
See product
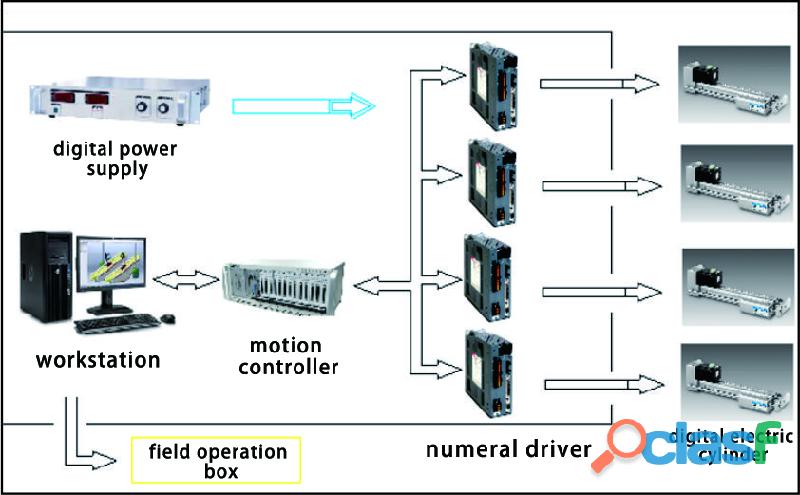
Pakistan (All cities)
Rs 0,0
See product
3 photos

Pakistan
Kennel Club Assured Breeder. Jimjen George Gently is a proven sire, (daughter & son Crufts qualified), and health tested, for MLS, NCCD, FVll, & IGS, and available at stud, to approved bitches,at small show kennel in Suffolk. 'Reach....Bonnie is a friendly and loving dog who loves attention and is very outgoing. He has been with us since he was 8 months old, but unfortunately he has been fighting with my male cat which causes him stress and anxiety being around the house.....Our amazing litter was born on 18th of December mum is stunning tri colour and dad is a lemon and white tri both pedigrees dad has five generations blood line with his papers to prove. We have a litter of 9 chunky playful pups all wormed and....
Rs 200,0
See product
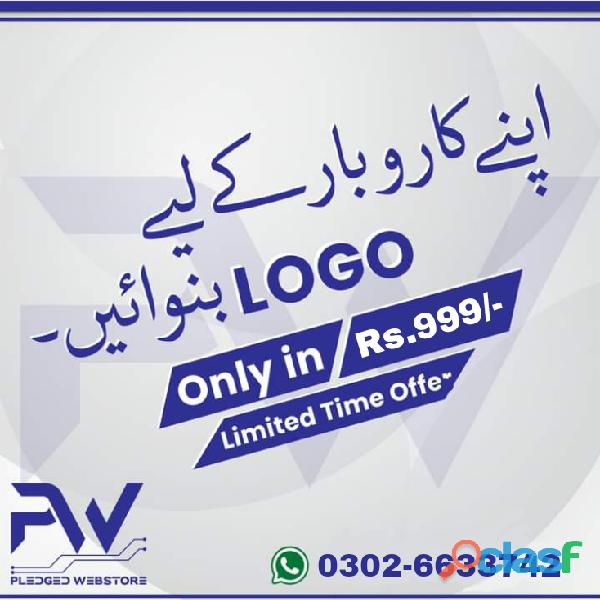
Gujranwala (Punjab)
I am a professional logo designer with 4 years of experience, specializing in creating unique and memorable brand identities. My expertise lies in designing logos that effectively communicate your brand’s values and vision. Over the years, I’ve worked with various industries, delivering tailored designs that stand out. I prioritize client satisfaction by ensuring clear communication and timely delivery. My design process is detail-oriented, combining creativity and strategy to create impactful logos. Whether you’re launching a new business or rebranding, I can help elevate your visual presence. Let’s collaborate to bring your ideas to life!
Rs 999,0
See product

Pakistan
due to a change in personal circumstances and a increase in work hours i am unfortunatly having to look for a new home for my four year old female beagle, jessie. Jessie has been spayed and is a member of the family it has been a very difficu....
Rs 200,0
See product

Pakistan
THE AMAZING HUGO & BOSS ARE LOOKING FOR THEIR FOREVER HOME. BOTH BOYS ARE LILAC IN COLOUR BUT ARE CARRIERS OF TAN POINTS WHICH IS THE AT GENE,DNA IS dd/bb/AT. PUPS ARE REALLY SHORT AND COBBY. GREAT CONFIRMATION, THE BEST WAY TO DESCRIBE THESE....
Rs 200,0
See product
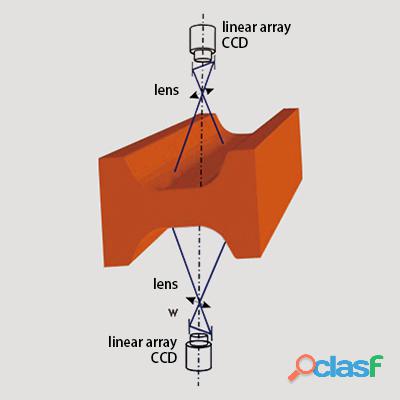
Pakistan (All cities)
Rs 0,0
See product