Kojie
Top sales list kojie

Latest Offers

Pakistan (All cities)
Manufacturer's Warranty. Tecno Industries (Reg) اَلحَمْدُ لِله Manufacturers of: SERVO MOTOR controlled, Automatic Voltage Stabilizers & Regulators. (pure copper) Since 1986 Tecno Lazer Pakistan. 0300-9433728 Ring Road, Band Road, Lahore Pakistan. A Servo Stabilizer That Decreases 30 Volts (back-from 250 to 220 & Increases 70 Volts from 150 to 220) (±) 1% {CAN STEP-UP from even low (on-demand)} اَلحَمْدُ لِله Runs your Equipment Even in Low Main Voltage. INFORMATION: 1: ( An Old Transformer / Relay carrying Stabilizer steps down or up after losing or gaining 20-25 Volts While A Servo Stabilizer steps down or up after losing or gaining 1 Volt. (±) 1%) 2: (on-demand) Buck-Boost Transformer Technology add-in 2kVA and above Models. Basically they work on DC Servo Motor Control system. Their efficiency is much better and its output voltage of either 110 or 220 AC or any required voltage, more-over TECNO 3Phase models up-to 500kVA ratings are manufactured against a confirmed order. 1 year warranty with parts. 100% genuine copper winding (GUARANTEED) Specs for (intelligent Voltage Stabilizer): SERVO MOTOR controlled, Automatic Voltage Stabilizers & Regulators. Input Voltage : 150 To 250 AC Output Voltage : 110v & 220v AC (±) 1% Frequency : 45 or 60 Hz Wave Form : Non-distorted Sine-wave Response Time : 25ms / V Efficiency : 95 % Power Factor : 0.95 Relative Humidity : 30% to 80% (without condensation) Temperature Rise : Less Then 50c Control System : DC. Servo Motor Insulation Resistance : More then 3M?? at 500V DC Tested : 1500 V We Manufacture Servo Motor Controlled Automatic Voltage Stabilizer, using Japanese technology, for UPS, Solar, AC Air-Conditioner, Split-Type, Window Type, (LCD/LED TV) Washing Machine, Treadmill, Photocopier Machine. Television, Music System, Refrigerators, Ultra sound Machines, Embroidery Machines, All Sensitive Equipment, Signalling Devices, CNC Machines, Air Conditioning Plants, Telecommunication Networks, Motor Loads, Data Processing Equipment, Bio Medical Equipment, Drives, PLC’s, Induction Heating, Hotels, Defence Application, Industrial Units, Lighting Loads, Residential/ Offices, Farm Houses, R & D Institutions, Mainline Stabilizers, Sophisticated Laboratory Equipment etc. Runs your Appliances Even in Low Main Voltage. وولٹیج سٹیبلائزر Standard Power Ratings Available in Single-Phase & 3-Phase: 500VA, 1kVA, 2kVA, 3kVA, 5kVA, 10kVA, 30kVA. Up-to 500kVA Punjab NWFP, KPK, & All Pakistan Cargo, Feel Free to Call: Rana Naeem Hammad. M.D. Tecno Industries (Pvt) Ltd Lahore. +923009433728
Rs 121,0
See product
11 photos
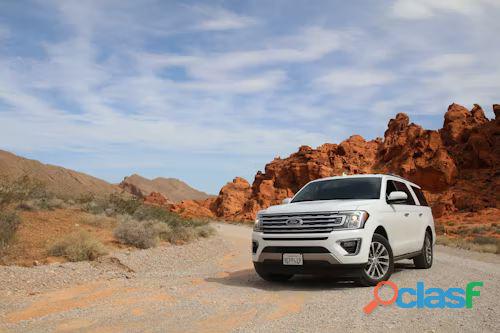
Lahore (Punjab)
Drive your dreams, rent with ease! With easy online booking and flexible rental options, you can confidently hit the road. https://www.rafaycars.com/
Rs 1.200,0
See product
3 photos
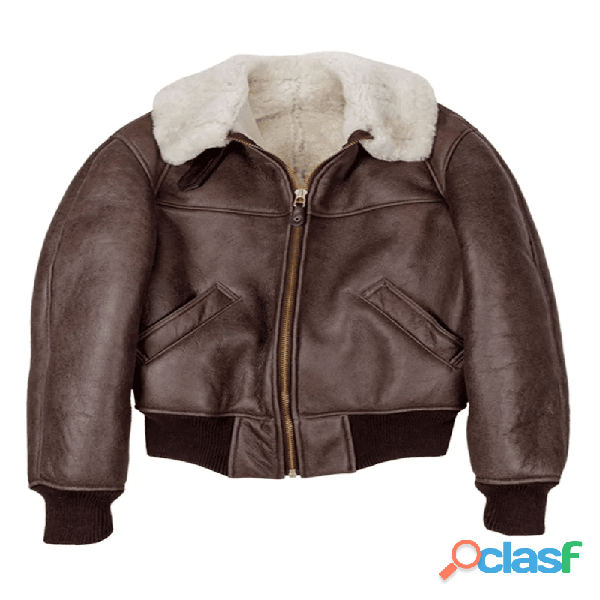
Pakistan (All cities)
The Veritable Calfskin store bring another Superstar Outfit Fur B-26 Shearling Aircraft Cowhide Coat. This Coat has been made by genuine quality Calfskin and has jazzy Fur Straight Style Collar https://aajacketmaker.com/product/b-26-shearling-fur-jacket/
Rs 70.000,0
See product
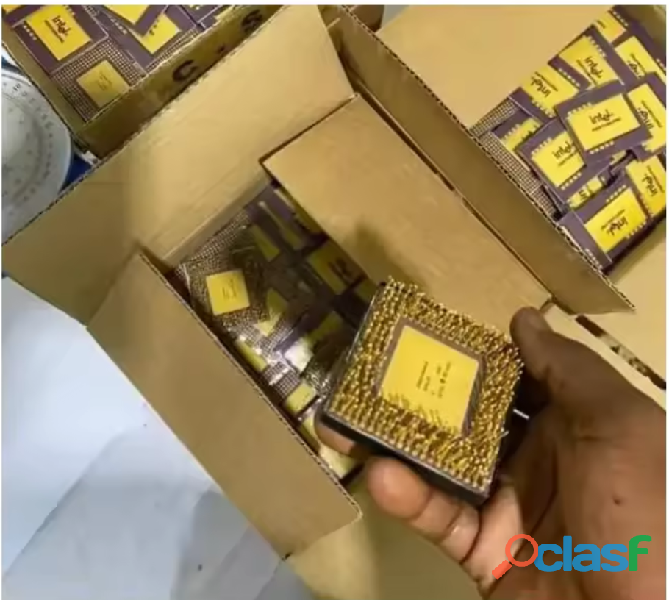
Pakistan (All cities)
We are specialized in the sales of full metal scrap/ recycling material such as ac/fridge compressor , Ceramic Cpu Gold Processor Scraps , H.M.S 1&2, Copper wire scrap,Drained Battery Lead scrap in the UK (LONDON).We have all our product fully ready for sales in good quantity and quality also to be shipped out for our buyers.For Booking : https://wa.link/og0sgp Whatsapp: +15806151130
Rs 1.000,0
See product
2 photos

Pakistan
2 pairs yellows for sale all in top condition ready for breeding they are 2015 bred birds 2 pairs yellows for sale all in top condition ready for breeding they are 2015 bred birds .....................2 pairs yellows for sale all in top condition ready for breeding they are 2015 bred birds
Rs 4.000,0
See product
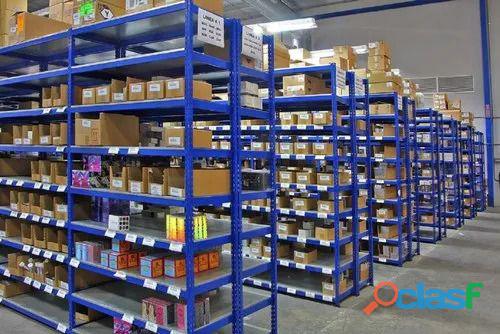
Bagh (Azad Kashmir)
Eagle Racking India is a leading provider of industrial storage racks in Kanpur, offering high-quality and durable storage solutions for warehouses, factories, and commercial facilities. Our storage racks are designed to maximize space utilization, enhance efficiency, and ensure easy inventory management. We specialize in a wide range of industrial racking systems, including pallet racks, heavy-duty racks, mezzanine racks, and cantilever racks, catering to diverse storage needs. Made from premium-grade steel, our racks are built to withstand heavy loads and provide long-lasting performance. They are designed with customizable shelving options, corrosion-resistant coatings, and high load-bearing capacities to meet industrial requirements Read more: https://eagleracking.com/kanpur/industrial-storage-rack
Rs 0,0
See product

Ahmadpur East (Punjab)
Sunshine Pest Control Pvt. Ltd offers expert waterproofing services to protect your home or business from water damage. We specialize in terrace, basement, and bathroom waterproofing using high-quality materials and proven techniques. Our solutions ensure long-lasting protection against leaks, dampness, and seepage. Choose our reliable services to keep your property dry, safe, and damage-free. Get in touch today for a free site inspection. Visit For More: https://pestcontrolsunshine.com/waterproofing-services/
Free
See product

Pakistan
I have a British blue shorthair male and female available for stud service. PKD NEGATIVE, BLOOD TYPE A or AB (CARRIER OF B). Tom had 8 litters so far, all healthy and chunky kittens. He is an indoor cat, fully vaccinated and in great health.
Rs 5.000,0
See product

Pakistan
Beautiful lemon and white female beagle pup for sale, 5 months old, fully vaccinated, microchipped, flee'd and wormed. Not kc registered and as she's our pet, mother or father can't be seen. Very playful, energetic and needs a caring family ....
Rs 200,0
See product

Pakistan (All cities)
FutureGenApps is a leading website designing company in Laxmi Nagar. We help businesses to grow online with our expert services such as web design and development, software development, website maintenance, social media marketing, SEO services, and e-commerce websites. Our experts provide a user-friendly and mobile-responsive websites that attract customers and enhance your business. We also maintain your site after it goes live, ensuring you remain stress-free. Whether you're a small start-up or a growing brand, FutureGenApps is here to support your online journey with effective and affordable solutions. Contact FutureGenApps now to get your top-notch website.
Free
See product
2 photos
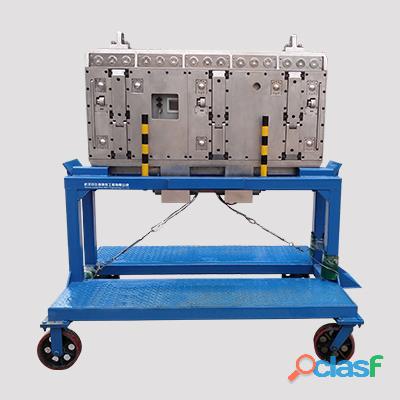
Pakistan (All cities)
Overview In order to ensure the quality of the slab, it is necessary to strictly control the performance and various parameters of the CCM’s guide roll within a certain error range. Due to the continuous casting machine (CCM) is large and in a harsh production environment, it is difficult to measure the performance of the continuous casting machine manually, and many parameters are difficult to measure. Therefore, it is very important to have a set of equipment that can simulate drawing of steel billet to realize the measurement of CCM’s various parameters and performance. The multifunctional strand condition monitor uses various sensors to realize the measurement of CCM’s roll gap value, the arc value of continuous casting section, the rotation quality of the rolls, and the water spray pressure under the condition of simulating drawing of steel billet. Therefore, the CCM’s quality can be controlled in real time, and it is convenient for the maintenance personnel to analyze the CCM’s measurement results. The problem areas of the casting machine equipment can also be found. If these problems doesn’t be found in time, it will cause the bad quality of CCM’s products, the steel breakout in pouring process, surface and internal cracks and centerline deviation. The measurement of the strand condition monitor Roll gap value: By measuring the distance between a series of inner arc guide rolls and outer arc guide rolls on the CCM’s roller bed. It can be used to set the correct roll gap spacing for each pair of guide rolls in the slab caster. Arc condition of guide roller : Measuring the position between the position of the CCM’s outer arc guide roll and the two adjacent guide rolls and then measuring the deviation compared with the origical position of CCM’s guide roll, we can obtain the arc condition of the outer arc guided roller. Guided roller rotation: It is possible to know whether each guided roller can rotate freely by measuring. Water spray pressure: The operation of the water spray cooling system can be judged by measuring the situation of secondary cooling water spray at different positions of CCM's width direction. Then we can accurately locate whether the water spray at a certain point is normal. The main components of the strand condition monitor 1. The main body of the strand condition monitor used to measure the continuous casting sector 2. The connecting chain between strand condition monitor and dummy bar 3. The storage rack chain of strand condition monitor 4. Battery charger: 24V 5A 5. Calibration equipment 6. Remote control 7. Laptop 8. Printer 9. Data communication cable The technical parameter 1. The measurement range of roll gap: 210mm, 230mm (can be customized according to requirements) 2. The measurement accuracy of roll gap: 0.01mm 3. The arc measurement range: ±80° 4. The arc measurement accuracy: 0.01° 5. The spray measurement range: 0-10 6. The spray measurement accuracy: ±1 7. The battery usage times: 3 times
Rs 0,0
See product

Pakistan (All cities)
The composition of the system The photoelectric strip automatic center position control system is mainly composed of sensors, amplifiers, PLC controllers, hydraulic control and other parts. System composition block diagram The main technical parameters 1. Detection width: 300-2800mm 2. Detection light source: 220VAC. (100VAC) 30W. High frequency white light works continuously 3. Photodetector: precision die-casting components, time constant 20ms 4. Maximum working voltage: 50VDC 5. Distance from receiver to emitter: 300-1000mm 6. Operating temperature: 0℃-60℃ 7. Resolution: 0.5mm 8. Linearity: ±1%F.S (after linearization) 9. Repeatability error: △R1%, F.S 10. Servo-valve working signal: ±10V 11. Rated pressure (oil pressure): 4.5Mpa 12. Rated flow: 30L/min 13. Symmetry: 10%
Rs 0,0
See product
2 photos
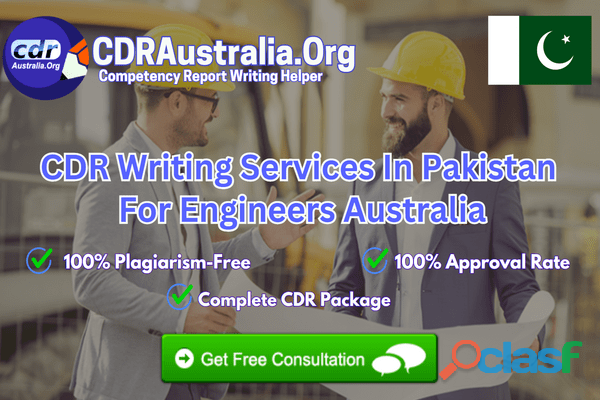
Sialkot (Punjab)
Feeling intricacies in crafting a CDR application for Engineers Australia’s skills assessment? Do not worry; order CDR Writing Services in Pakistan for Engineers Australia. It is the best-known online writing assistance for CDR applicants in Pakistan. CDRAustralia.Org offers such commendable support to meet aspirants' requirements. The service comprises a complete CDR package from selecting projects to writing career episodes, a summary statement, a CPD statement, and a resume. To guide candidates in framing an EA-acceptable competency assessment report, a brilliant team of professional writers is awaiting. Expert writers offer comprehensive assistance to make the report extraordinary so that it can catch EA’s attention and undergo successful assessment. Hire top experts at CDR Australia and relieve all your writing woes. Hired native writers offer CDR support tailored to your requirements and meet all Engineers Australia standards. If you seek any information regarding the services, contact our experts free of cost by visiting the website. Contact Detail: Website: https://cdraustralia.org/pk/ Mail at: Contact@CDRAustralia.Org WhatsApp: +61-291917405
Rs 2.784.000.000,0
See product
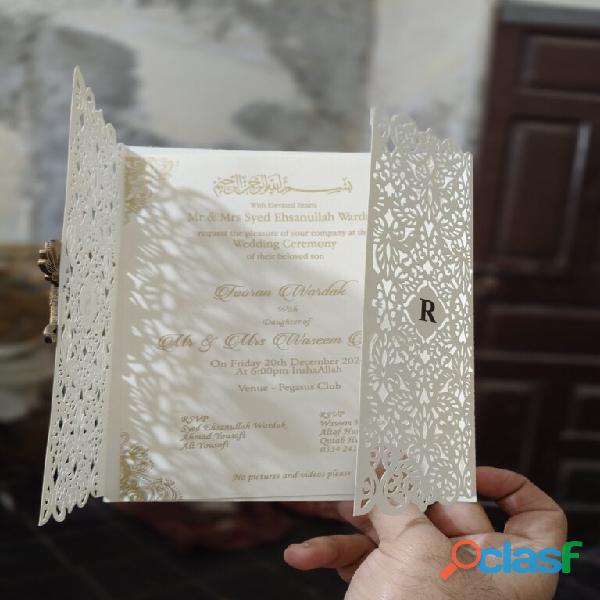
Pakistan (All cities)
Wedding Cards Manufacturing in Pakistan, Pakistani Wedding Cards, Wedding Cards from Pakistan, Favour Boxes Pakistan, Nikkah Boxes Pakistan, Bid Box Pakistan, Bidh Box Pakistan, Customized Wddding Cards Pakistan, Wedding Cards Lahore, Wedding Cards Pakistan, Acrylic Wedding Cards, Wax Stamp Wedding Cards, Bes Cards https://cardnboxes.com/
Rs 100,0
See product

Pakistan (All cities)
Overview The taper of the narrow face of the mold has an important influence on the quality of the casting billet. Excessive taper will cause the mold to squeeze the billet shell, and a small taper will increase the air gap. With the continuous increase of the requirements of the casting billets’ quality and the continuous introduction of high-precision molds, the current taper measuring instrument in the domestic market generally have low measurement accuracy and complex measurement methods, which restrict production development. The new-generation taper measuring instrument developed by Wuhan CenterRise M&C Engineering Co., Ltd. adopts imported high-precision inclination sensor, combined with ultra-low power consumption processor, which can quickly and accurately measure the actual taper value of the narrow copper plate of the mold. The instrument is fully functional, easy to use and suitable for slab molds of various lengths. Most of the current slab molds are single-taper, a narrow flat copper plate. The taper value required for production can be achieved by adjusting the angle between the narrow copper plate and the direction of gravity. The taper measuring instrument directly measures the angle between the narrow copper plate and the direction of gravity. According to habits and production needs, the angle is converted into the value of one-sided shrinkage of the upper and lower ports. The main features 1. Easy to calibrate, stable performance, easy to operate 2. Self-supporting, self-aligning, self-balancing 3. High measurement accuracy 4. LCD data reading 5. Fast response, real-time display reading 6. Adjustment of dynamic intelligent system 7. Lithium battery power supply, suitable for on-site use of mobile operations 8. The continuous measurement time is more than 36 hours 9. The sensor adopts multiple protections to meet the needs of on-site harsh environment measurement 10. The weight of the whole system is less than 3.8 kg, and it is equipped with a set of zero-point calibration table, which is convenient for on-site installation and measurement 11. Applicable to various arc, parabolic and straight molds The performance and index 1. Measuring range: -3°~ +3° (measurement length can be customized according to users’ needs) 2. Measurement accuracy: 0.01mm 3. Temperature range: -25℃~+85℃ 4. Linearity deviation: -0.03mm ~ + 0.03 mm 5. The longest usage time after fully charged: 36 hours 6. The longest storage time after fully charged: 2 months The main components 1. Measuring instrument: central measurement and control unit, measuring sensor 2. Measuring stand 3. Standard table: standard surface, support frame, spirit level
Rs 0,0
See product