Dany tv toner fm
Top sales list dany tv toner fm

Latest Offers

Pakistan (All cities)
Get the best nail polish services in Hyderabad at Kameleon Salon, from classic manicures to gel finishes.
Free
See product

Pakistan (All cities)
FutureGenApps is a leading website designing company in Laxmi Nagar. We help businesses to grow online with our expert services such as web design and development, software development, website maintenance, social media marketing, SEO services, and e-commerce websites. Our experts provide a user-friendly and mobile-responsive websites that attract customers and enhance your business. We also maintain your site after it goes live, ensuring you remain stress-free. Whether you're a small start-up or a growing brand, FutureGenApps is here to support your online journey with effective and affordable solutions. Contact FutureGenApps now to get your top-notch website.
Free
See product
2 photos
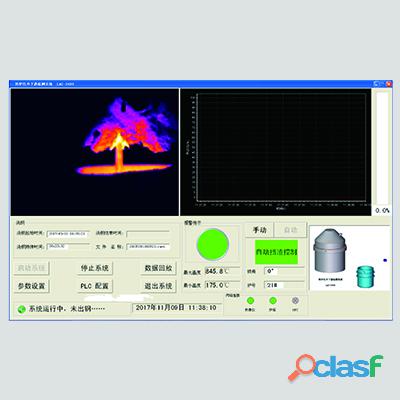
Pakistan (All cities)
Overview The infrared converter slag detection system uses a far-infrared thermal imager to monitor the situation of converter tapping in real time, and is connected to the main control computer in the electrical room through the conversion and transmission of video signals. The radiation intensity in the infrared wavelength range of 7-14um is different to distinguish molten steel and slag. In the later stage of the converter tapping, the molten steel gradually decreases, and the steelmaking slag is involved in the molten steel and flows out of the tapping hole. After the thermal imager recognizes the steelmaking slag in the imaging temperature measurement, it will give an alarm according to the slag content ratio threshold set by the software. The thermal imager will start the slide plate to close the tapping hole, so as to realize the control of the slag in the converter tapping, and ensure the maximum yield of molten steel and the minimum control of the steelmaking slag content. The effect of slag detection in converter tapping is of great significance to the control effect of the slag amount. The converter slag detection and control system developed by our company conducts non-contact monitoring of the tapping steel flow through the far-infrared detector thermal imager. It can detect the slag condition in real time and output an alarm signal and control system, which can replace manual visual inspection and provide accurate, efficient and stable slag detection effect. When the system finds the slag, the intelligent control unit quickly makes a judgment of lifting the furnace and blocking the slag and outputs an alarm signal. As shown in Figure 1, the system includes thermal imager, front purge protection box, front electrical box, power distribution cabinet, main control monitor, monitor of rocking furnace chamber, sound and light alarm, infrared converter slag monitoring software system, etc. The features of thermal imager 1. The temperature measurement range is 200°C ~ 2000°C, high temperature measurement accuracy, and multiple temperature measurement intervals can be set. 2. High-resolution thermal imaging system, the imaging picture is clear, and the imaging color can be freely marked according to the set temperature. 3. With hot zone alarm function, the alarm zone and temperature range can be set arbitrarily. 4. With hot zone tracking function 5. Equipped with special 7~14um infrared filter lens The technical parameters 1. Temperature measurement range: 200°C ~ 2000°C 2. Temperature measurement accuracy: 2% 3. Detection accuracy and alarm accuracy: ≥98% 4. Resolution: ≥ 0.5℃ 5. Pixels: 640x240PT 6. Band: 7~14um 7. Field of view: 7.5°×5.5° 8. Frame rate: ≥ 25 frames/sec 9. Equipment service life: ≥5 years 10. The normal operation rate of the automatic control system: ≥99%
Rs 0,0
See product
3 photos
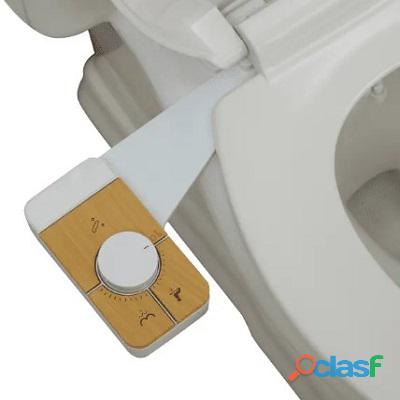
Pakistan (All cities)
Topper Smart Bidet Tiolet Seat Co., Ltd. (https://www.mfrsbidet.com/) is a professional and experienced smart toilet & bidet manufacturer and supplier, specializing in diversifying our bidet products to suit a range of different needs. We are capable of providing toilet bidets, bidet attachments, bidet seats, toilet seat covers, bidet sprayers, portable bidets and other bidet fittings, and offering practical and personalized sanitary solutions for our customers. Over the years, we have been consistent in supplying high-quality products and thoughtful services. Every stage in the production is guided and supervised by skilled professionals and our quality control systems. Our bidet products all meet tangible and intangible requirements in terms of quality and safety. From the design and development of products to the user experience, we are never slackening our effort, and still trying our best to improve your life quality. Convenience, comfort and superior quality are the ideas we want to convey through our bidets and services. In the future, we will continue to strengthen our capability of design and innovation to better satisfy the demands of the market and create the best home life experience for customers. If you're interested in our bidets, please visit https://www.mfrsbidet.com/.
Rs 200,0
See product
6 photos
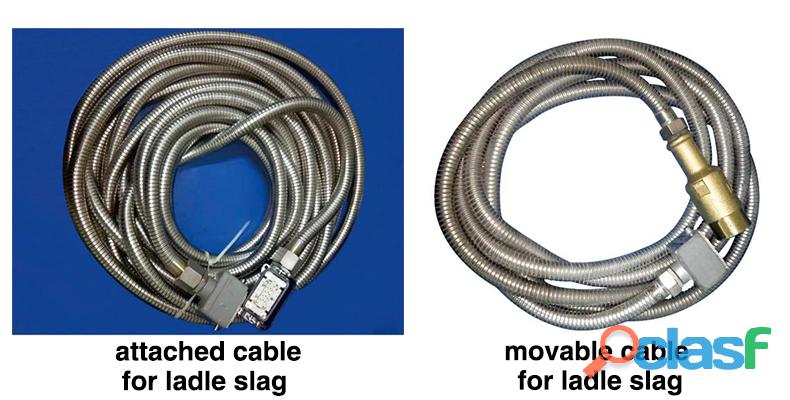
Pakistan (All cities)
Overview Our company focuses on the production and application of the cables in continuous casting steel production. We have rich on-site usage experience, which provides us with technical guarantees for manufacturing high-quality communication cables. For cables of different applications, we have different protection requirements, such as high temperature resistance, anti-pull, acid and salt spray resistance, slightly positive pressure heavy-duty connector, anti-oil pollution, anti-interference, etc. Common industriaI cable for continuous casting 1. Breakout prediction compensation cable 2. Mold level control cable 3. Mold oscillation cable 4. VUHZ sensor cable 5. Mold width adjustment cable 6. Dynamic lightly depress the cable 7. Fixed cable for ladle slag 8. Movable cable for ladle slag The quality control All our products use proven materials to ensure stable and reliable product quality from the source. The core equipment all adopt imported raw materials. From raw material control to wire harness integrated processing, we ensure the stability and consistency of product quality. The scientific quality management system brings the product quality to a higher level. The program customization Our company has been focusing on the production and processing of wire harness products for many years. We have a professional technical team, which can realize synchronous development and technical docking with customers timely, optimize product design, and provide customers with complete solutions for wire harness products. Widely used: All kinds of wire harnesses produced by our company are widely used in major steel mills across the country, such as SHOUGANG, TISCO, HBIS GROUP, TIANJIN IRON PLANT, BAOGRANG GROUP, etc. The first-class product quality, and has won unanimous praise from domestic and abroad.
Rs 0,0
See product
5 photos

Pakistan
due to a change in personal circumstances and a increase in work hours i am unfortunatly having to look for a new home for my four year old female beagle, jessie. Jessie has been spayed and is a member of the family it has been a very difficu....
Rs 200,0
See product
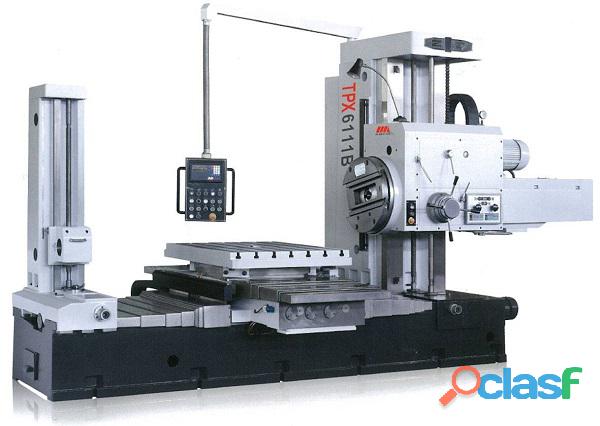
Pakistan (All cities)
Explore the leading manufacturers of horizontal and vertical boring machines, renowned for their precision engineering, innovative technology, and reliable performance. This guide covers top companies offering high-quality machines for various industries, including construction, mining, and manufacturing. Discover key features, advantages, and the latest trends in boring machine design. Whether you're seeking new or used equipment, find trusted suppliers to meet your project needs with ease. https://www.tradebrio.com/exporters/boring-machine.html
Free
See product

Pakistan
Beautiful lemon and white female beagle pup for sale, 5 months old, fully vaccinated, microchipped, flee'd and wormed. Not kc registered and as she's our pet, mother or father can't be seen. Very playful, energetic and needs a caring family ....
Rs 200,0
See product

Pakistan (All cities)
GoLogica offers complete online training in data modeling that gives professionals the understanding and skills they need to understand data modeling methods. IT specialists, database developers, business analysts, and data analysts who want to become better in creating and managing data structures may benefit from this course. Basic topics covered in the course include entity-relational diagrams (ERDs), data mapping, normalization strategies, and abstract, logical, and physical data modeling. It also covers database design concepts, demonstrating how to build durable, scalable, and effective data models that correspond with business goals. This course, led by industry experts, gives participants practical knowledge through practical assignments, allowing them to apply what they've learned in actual situations. Whether you're new to data modeling or want to improve your existing skills, GoLogica Data Modeling Online Training provides a solid basis for creating and managing successful data models. Enroll in GoLogica Data Modeling Online Training today to obtain the knowledge you need to boost your career in data management and become a certified Data Modeling expert!
Rs 0,0
See product

Pakistan (All cities)
Overview The system realizes the fixed-length measurement of the width, thickness and length of the continuously cast product through machine vision and laser rangefinding system. The measured data is transmitted to the host system through the optical fiber. The host system calculates the weight of each billet according to different steel grades and specific gravity, so that we can realize the fixed length measurement and fixed weight control of the cast products and the precise control of the steelmaking process in the production process. After cutting the billets by fixed weight and length, the fixed weight cut-to-length system is checked by the online weighing measurement system, so as to give feedback to the fixed length model of control system. The slab number (automatic checking) can also be automatically identified online by using machine vision, and the weight and slab number can be automatically stored in the local database for use in the production and management system. The measuring principle of the system On the upper surface of the billet, a set of linear CCD cameras and a laser rangefinding instrument are respectively installed. Through machine vision and laser correction, we can achieve precise measurement of the cast products’ shape. Through accurate cast products’ shape monitoring, the billet thermal expansion coefficient of cast products and cast products’ density at the current temperature, we can obtain the quality of the billet. At the same time, we can achieve high-precision quality cut-to-length , namely, fixed-weight and fixed-length. The system can be matched with the weight detection and calibration system. The system adopts the online barrier-free hidden integral roller table weighing method for continuous casting products, and connects its weighing data into the intelligent control model. The model and steel billet weighing system, and the fixed weight cut-to-length system realize the closed-loop control of the system model, and optimize the fixed weight accuracy through automatic signal collection. The features of the equipment The cutting control technology for fixed-length and fixed-weight of cast products is a concrete manifestation of the lean production management of steel products. In the era of high-quality competition of steel products, only high-end intelligent technology and management can reduce costs, improve quality and market competitiveness. 1. Data management can be carried out according to shifts, pouring times, days, weeks, months, etc., as well as data management according to specifications, production capacity, quality, etc. 2. Each stream can send out signals such as pre-clamping, clamping, cutting, roll-up, roll-down and return of the cutting car according to the user's requirements. 3. The detection and cutting precision is high, the controllable length sizing accuracy is ±1mm, and the quality sizing accuracy is more than 1.5‰. 4. It is not sensitive to other high-intensity light interference, and overcomes the influence of light sources such as sunlight and arc welding. 5. The monitor displays the running status of the current hot billet in real time and displays the corresponding parameters. 6. Laser rangefinding and CCD machine vision are used to calculate the weight of the cast products and optimize the cutting to length. 7. Historical cutting data is automatically stored, and the system can set rules for historical data. 8. Support the free transformation of fixed length, and a variety of operation modes are available for the operator to choose. 9. Adopt advanced high temperature laser measurement and high pixel linear CCD technology. 10. The system provides abundant interfaces, which can communicate with the PLC control. 11. Applicable to all kinds of continuous casting machine flame cutting system. 12. Provide automatic, upper and manual cutting control. The main technical requirements 1. Width range of the inspected cast product: 120~2000 mm 2. Length range of the inspected cast product: 1000~20000 mm 3. Thickness range of the inspected cast product: 35~400 mm 4. Steel billet moving speed: 3.5 m/s 5. Billet running speed: 6.5m/min 6. Temperature of the measured steel billet: 0~850 °C 7. Measurement accuracy: width ±0.2mm thickness ±0.2mm length ±0.2mm 8. Fixed weight accuracy: 0.8‰ (temperature model verification) 9. Quality inspection check: 1‰
Rs 0,0
See product

Pakistan
THE AMAZING HUGO & BOSS ARE LOOKING FOR THEIR FOREVER HOME. BOTH BOYS ARE LILAC IN COLOUR BUT ARE CARRIERS OF TAN POINTS WHICH IS THE AT GENE,DNA IS dd/bb/AT. PUPS ARE REALLY SHORT AND COBBY. GREAT CONFIRMATION, THE BEST WAY TO DESCRIBE THESE....
Rs 200,0
See product
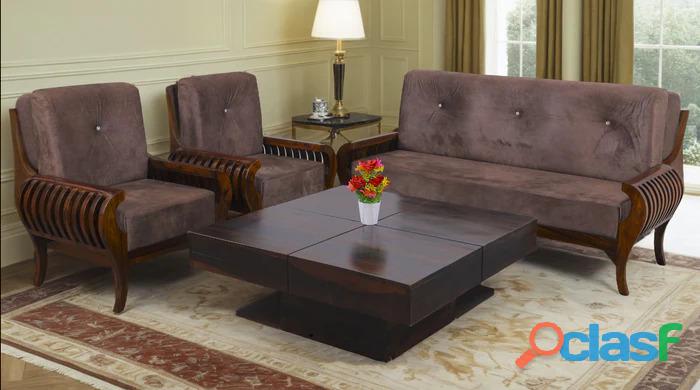
Gujrat (Punjab)
Jaipur, a city celebrated for its heritage and craftsmanship, is home to some of the finest Sheesham wood bed manufacturers. Sheesham wood, known for its strength, durability, and stunning natural grain patterns, is the ideal material for crafting high-quality beds that combine functionality with timeless beauty. Why Choose Sheesham Wood Beds? Durability: Sheesham wood is incredibly strong and resistant to wear, ensuring a long-lasting bed. Elegant Design: The rich textures and natural grain of Sheesham add a luxurious and earthy charm to any bedroom. Customizable Options: Jaipur manufacturers offer bespoke designs to suit your space and style preferences, from traditional carved beds to sleek modern styles. Eco-Friendly Choice: Many manufacturers use sustainably sourced Sheesham wood, supporting environmentally responsible practices. Types of Sheesham Wood Beds Available: Standard Beds: Classic designs suitable for any bedroom decor. Storage Beds: Functional beds with built-in storage to maximize space. Platform Beds: Minimalist and contemporary designs for a modern look. Poster Beds: Elegant four-poster beds that bring a royal touch to your space. Customized Beds: Tailored designs to fit specific dimensions and styles. Why Choose Sheesham Wood Bed Manufacturers in Jaipur? Jaipur’s Sheesham wood bed manufacturers are known for their impeccable craftsmanship, attention to detail, and the ability to deliver high-quality products. With a focus on both aesthetics and functionality, they ensure each bed is not only a piece of furniture but also a work of art. Explore the collections from Jaipur’s top Sheesham wood bed manufacturers and bring home a bed that combines luxury, comfort, and durability for a perfect night’s rest.
Rs 54.651,0
See product
2 photos
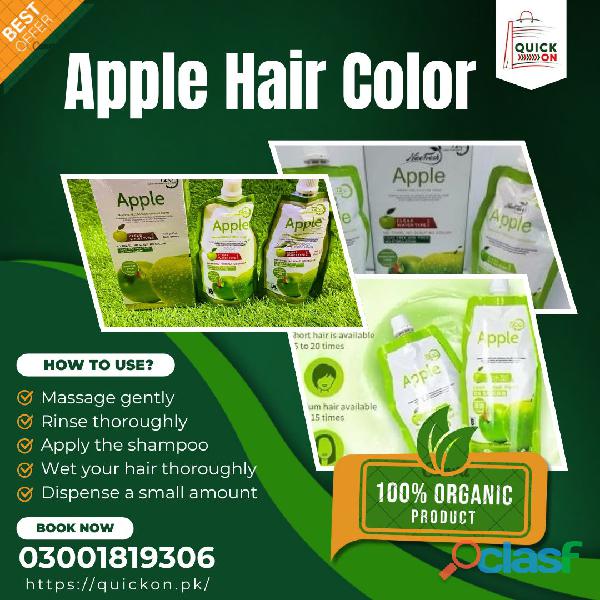
Islamabad (Islamabad Capital Territory)
Apple Hair Color Price In Pakistan - Quickon.pk Apple Hair Color PriceIn Pakistan offers a natural and effective solution for achieving vibrant, long-lasting hair color while maintaining the health and integrity of your hair. With its blend of conditioning agents and natural extracts, it provides a nourishing and protective coloring experience. By following the usage instructions and being mindful of potential side effects, users can enjoy salon-quality results in the comfort of their own home. Whether you are looking to refresh your current color or try a new shade, Apple Hair Color Price In Pakistan is a valuable addition to your hair care routine. FAQs About Apple Hair Color Price In Pakistan: What is Apple Hair Color? Apple Hair Color is a natural hair dye formulated with ingredients derived from apples and other natural sources. It is often used as an alternative to chemical hair dyes. Is Apple Hair Color safe for all hair types? Apple Hair Color is safe for all hair types. Does Apple Hair Color contain any harsh chemicals? Apple Hair Color is usually free from harsh chemicals like ammonia and parabens, making it a gentler option compared to conventional hair dyes. How long does Apple Hair Color last? The longevity of Apple Hair Color varies depending on the hair type and care routine. On average, it lasts for 4-6 weeks before fading. Can Apple Hair Color cover gray hair effectively? Yes, Apple Hair Color can cover gray hair, although the coverage may be less intense compared to synthetic dyes. Multiple applications might be needed for full coverage. Is Apple Hair Color suitable for sensitive scalps? Apple Hair Color is often marketed as suitable for sensitive scalps due to its natural ingredients. How should I prepare my hair before applying Apple Hair Color? It's recommended to wash your hair with a mild, sulfate-free shampoo and avoid using conditioner before applying the hair color for better absorption. Can I use Apple Hair Color on chemically treated or colored hair? Yes, Apple Hair Color can be used on chemically treated or colored hair. How often can I reapply Apple Hair Color? You can reapply AppleHair Color every 4-6 weeks, or as needed, to maintain the desired shade. Are there any special aftercare instructions for Apple Hair Color? To prolong the color, use sulfate-free shampoos, avoid excessive heat styling, and protect your hair from direct sunlight. For more details: WhatsApp: +923001819306 Website: quickon.pk Product Link: https://quickon.pk/ https://quickon.pk/product/apple-hair-color-price-in-pakistan https://quickon.pk/product/luvvel-hair-darkening-shampoo-price-in-pakistan https://quickon.pk/product/navratna-oil-price-in-pakistan https://quickon.pk/product/german-hair-color-gel https://quickon.pk/product/zinc-shampoo-price-in-pakistan https://quickon.pk/product/catherine-slimming-tea https://quickon.pk/product/lichen-hair-color-gel
Rs 3.500,0
See product
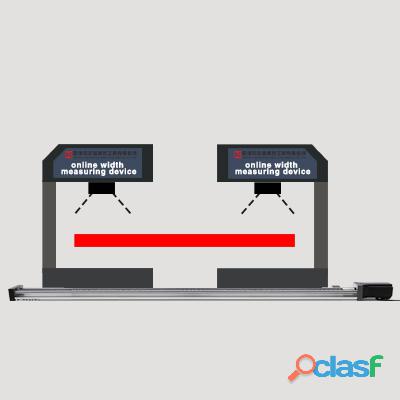
Pakistan (All cities)
Overview The WGS-L200 Laser Slab/ Plate Steel Width Measuring System adopts the principle of double laser triangulation reflection to process the online measurement of the steel plate on the roller bed, and combines the high-speed digital signal processing technology and programming software to process the signal correspondingly, and displays the relevant data and measurement curve, so as to realize the accurate control for steelmaking process during the production. The WGS-L200 Laser Slab/Plate Steel Width Measuring System is mainly composed of computing processing software and hardware systems such as testing equipment, computing equipment. The hardware system consists of 2 sets of laser triangulation rangefinding system, on-site signal acquisition and transmission system, operation unit, host analysis and control alarm system, etc. The software of WGS-L200 laser slab/ plate steel width measuring system mainly includes data acquisition and analysis, alarm software and data visualization operation software in the host system. The data analysis system analyzes and converts the data transmitted by the signal acquisition and analysis system into the visual data of the main control room, and completes the width measurement monitoring work in the slab production operation through the set alarm threshold. The measuring principle of the system The WGS-L200 Laser Slab/Plate Steel Width Measuring System is mainly composed of computing processing software and hardware systems such as testing equipment, computing equipment. The hardware system consists of 2 sets of laser triangulation rangefinding system, on-site signal acquisition and transmission system, operation unit, host analysis and control alarm system, etc. The software of WGS-L200 laser slab/ plate steel width measuring system mainly includes data acquisition and analysis, alarm software and data visualization operation software in the host system. The data analysis system analyzes and converts the data transmitted by the signal acquisition and analysis system into the visual data of the main control room, and completes the width measurement monitoring work in the slab production operation through the set alarm threshold. The features of the system 1. Using the principle of laser triangulation reflection, it is very suitable for dynamic measurement, and the dynamic measurement accuracy is high. 2. Non-contact type, namely, the laser rangefinding sensor is installed on the upper and lower sides of the strip conveying guide groove, and the width measurement device is not in direct contact with the strip. 3. Continuous and fast sampling measurement, the sampling frequency is 300Hz-2000Hz. The measurement frequency can be set freely to realize high-speed width detection. 4. It can effectively identify and compensate the beating, inclination, side deflection and profile of the tested plate; 5. Excellent mathematical model realizes accurate width detection of the bad profile; 6. The software interface is good, powerful, easy to operate and maintenance-free; 7. The software has self-diagnosis function; 8. Full digital detection, automatic calibration system; 9. High measurement accuracy and fast response; 10. Using optical fiber signal transmission; 11. Quality control alarm; The technical parameters Measuring distance: 0.5-0.8m (according to the on-site environment) Resolution: ±0.1mm Repeatability: 0.2mm Measurement output frequency: 100-3KHz Laser class: 2 (IEC60825-1:2014) Protection class: IP65 Communication method: TCP/IP communication
Rs 0,0
See product

Pakistan (All cities)
Get professional lawyer app development, lawyer consulting app development, and lawyer finder app development services with Dev Technosys. We create secure, user-friendly legal apps tailored to your needs. Enhance client engagement, manage cases efficiently, and streamline legal services. Contact us today for reliable and innovative legal tech solutions.
Rs 0,0
See product